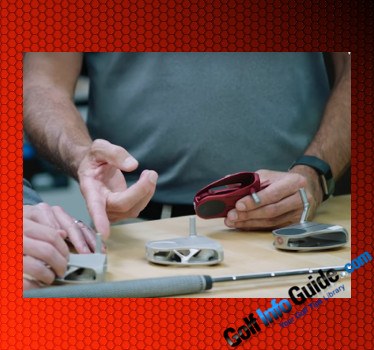
Callaway’s Odyssey R-Ball is going to get a major upgrade, as the company announced recently that it has signed a collaboration/consultancy agreement with General Electric’s Additive’s AddWorks team. The joint venture between the two companies is aimed at improving Callaway’s gear manufacturing technology via General Electric’s patented Additive Manufacturing, a high-tech innovation that uses digital design to create physical objects, thus facilitating the manufacturing of stronger and lighter systems and parts. With regard to Callaway’s equipment, this translates into a redesigned/re-engineered
Odyssey R-Ball Prototype putter head, which is highly popular in Japan, where it has been developed originally as a tour-preferred design. The Odyssey R-Ball Prototype putter head design is kind of peculiar, as it removes the front ball, compared to the initial 2-ball design. The new additive manufacturing technology, which is to be employed by Callaway soon in their Odyssey R-Ball Prototype, will optimize the putter’s acoustics, while keeping its original and hugely popular shape, without sacrificing performance in the process. The director of Callaway’s Research and Development/Advanced Engineering, Brad Rice respectively, has been quoted as saying that the technology borrowed from General Electric is going to be the golf industry standard in the future, in regard to manufacturing golf equipment:
“Additive manufacturing is a new tool; which is quickly going beyond the aspirational phase, and into the functionalization phase of the technology. Callaway needs to learn how to use this tool well because it is inevitable that 3D-Printing of production parts is going to happen – it is the production method of the future.”
Here’s a cool video about the joint-venture between General Electric and Callaway, working at creating the perfect acoustics on the latter’s R-Ball Prototype putter head. How are they going to do it, you asked? Well, this cutting edge technology enables better designs compared to the traditional casting methods, allowing Callaway to create a putter which boasts optimal shape and design, together with the ideal acoustic signature the brand aficionados know and love. According to Chris Schuppe, General Electric’s Additive AdWorks general manager, this is just the first step of additive manufacturing entering the golf-world, and we’re definitely going to hear more about it in the near future:
“We’re taking away many new learnings from our first project together, especially around aesthetics. We have also used additive technology to create an acoustic map, which is certainly a first for us. We’re looking forward to driving more successful projects with Callaway, as they continue their additive journey.”
It’s interesting to note that EBM or Electronic Beam Manufacturing is for the most part a bought up technology from a Swedish company called Arcam, that is now a part of GE. It’s actually fun to see 3D-printing technologies getting a wider audience. Rapid prototyping might soon translate into rapid(and local) production of everything, including golf equipment, or whatever. Now, wouldn’t that be a thing ? Where all your golf-clubs are not produced in Taiwan by a multinational corporation, but in the neighboring town? Supporting local business and less shipping? At a fraction of the cost? The future sounds interesting.